How Fiber Optic Cable Factories Can Reduce Their Carbon Footprint
How Fiber Optic Cable Factories Can Reduce Their Carbon Footprint
In today’s world, the drive toward sustainability is reshaping industries, including those involved in advanced technologies like fiber optics. As the demand for high-speed internet and data transmission continues to soar, so too does the need for the manufacturing of fiber optic cables. But with manufacturing comes environmental responsibility. Reducing the carbon footprint of fiber optic cable factories is not only critical for addressing climate change but also offers operational and cost-saving benefits for businesses.
Here’s how Jera Line factory can significantly reduce their carbon footprint while maintaining production efficiency and supporting the global transition toward greener technologies.
Manufacturing fiber optic cables is energy-intensive, especially in processes like extrusion, coating, and curing. To tackle this, Jera Line factory can:
● Adopt energy-efficient machinery: Upgrading to the latest energy-efficient manufacturing equipment can drastically reduce energy consumption. For example, more efficient extrusion machines consume less power while maintaining high output levels.
● Switch to renewable energy sources: Installing on-site solar panels, or partnering with local wind or hydroelectric power providers, can drastically cut emissions associated with traditional energy sources like coal and natural gas. Many forward-thinking factories are already shifting to 100% renewable energy to power their operations, significantly reducing their carbon footprint.
● Leverage heat recovery systems: Manufacturing processes often generate excess heat, which can be recovered and reused. Factories that invest in heat recovery systems can capture this energy and repurpose it for other processes, reducing overall energy consumption.
2. Sustainable Materials
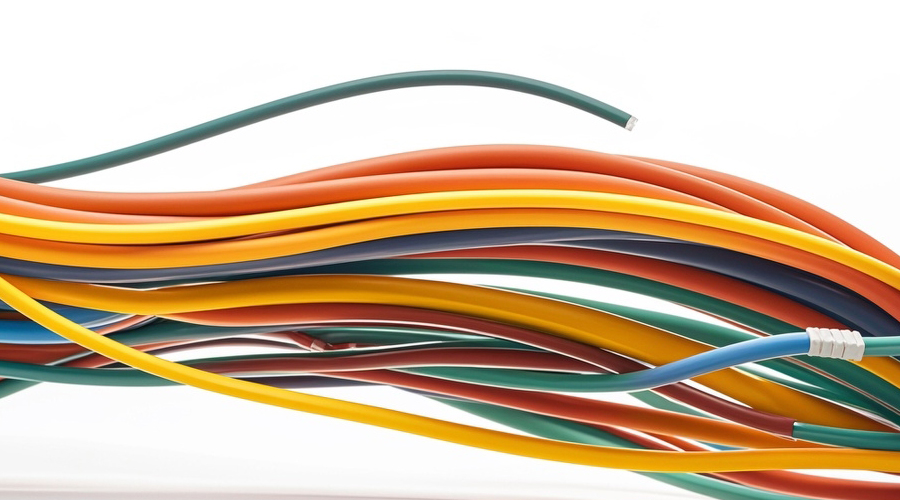
A key factor in reducing the carbon footprint lies in the materials used in the cables themselves. Traditionally, the plastic coatings and sheaths used for fiber optic cables are derived from petroleum-based products. By shifting toward more sustainable alternatives, Jera Line factory can minimize their environmental impact:
https://www.jera-fiber.com/about-us/guarantee-responsibility-and-laboratory/
● Bio-based or recycled materials: Using eco-friendly alternatives, such as biodegradable plastics or recycled polymers, reduces reliance on virgin raw materials and lowers the carbon emissions associated with their production. Some cutting-edge manufacturers are already experimenting with bio-based polyethylene and other sustainable materials for cable insulation and jackets.
● Minimizing material waste: Advanced production techniques, like precision cutting and laser-guided measurement systems, ensure that raw materials are used as efficiently as possible, reducing offcuts and scrap materials. Not only does this cut down waste, but it also means less energy is expended producing unnecessary materials.
3. Smart Manufacturing Technologies
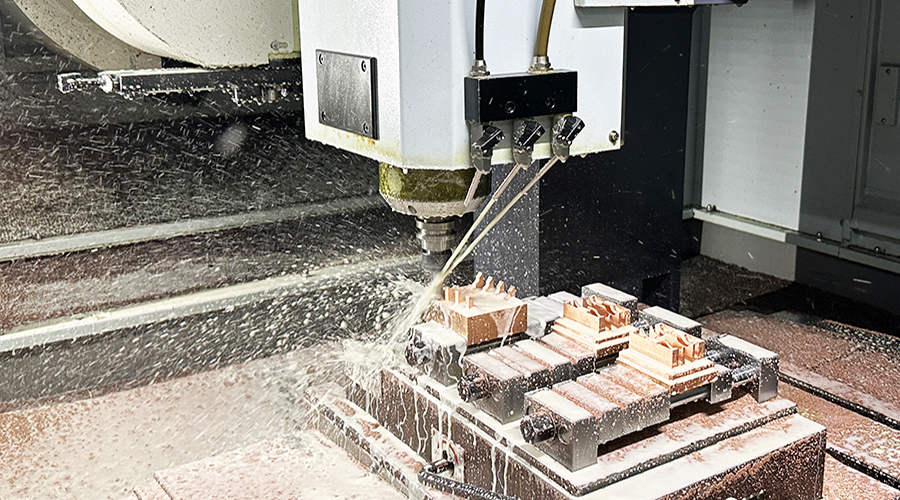
Technology can play a huge role in optimizing production processes and minimizing energy usage. Smart manufacturing solutions, driven by data and automation, can help Jera Line factory reduce emissions:
● IoT and AI-based automation: The Internet of Things (IoT) and artificial intelligence (AI) allow factories to track energy usage in real time, predict maintenance needs, and optimize production efficiency. AI algorithms can analyze production data and recommend more efficient ways to operate machines, thereby reducing energy use and carbon emissions.
● 3D printing and additive manufacturing: Although primarily associated with other industries, 3D printing has potential applications in fiber optic manufacturing, especially for creating precise parts and components with minimal waste. This reduces the need for excess material, driving down emissions related to material production and disposal.
4. Jera Line factory Recycling and Circular Economy Practices
A factory’s sustainability journey doesn’t end when a product leaves the facility. A holistic approach to reducing carbon footprints involves circular economy principles, which aim to eliminate waste and make the most of available resources.
● Cable recycling programs: Introducing recycling programs for old or decommissioned fiber optic cables can help recover valuable materials like glass fibers and metals. These materials can be reprocessed and reused in new cables, reducing the need for virgin materials and the emissions associated with extracting them.
● Circular water management: Factories often use significant amounts of water for cooling purposes during manufacturing. Implementing closed-loop systems that recycle and reuse water can greatly reduce consumption and the carbon footprint associated with water treatment and waste management.
5. Optimized Supply Chains and Green Logistics
The carbon footprint of fiber optic cable factories is not limited to the production floor. The transportation of raw materials to the factory and the distribution of finished products also contribute to emissions. By optimizing supply chains and logistics, Jera Line factory can reduce these emissions:
● Local sourcing: Sourcing raw materials locally reduces the need for long-distance transportation, which is a major contributor to carbon emissions. By partnering with local or regional suppliers, factories can reduce transportation emissions significantly.
● Electric and hybrid transportation: Using electric vehicles (EVs) or hybrid trucks for transporting raw materials and products can further reduce carbon emissions in the supply chain. More companies are adopting green logistics to minimize the environmental impact of shipping and distribution.
6. Durable and Energy-Efficient Products
Fiber optic cables themselves are more energy-efficient than traditional copper cables for transmitting data, as they require less power to maintain signal integrity over long distances. However, factories can still enhance this energy efficiency:
● Long-lasting products: By designing more durable fiber optic cables that last longer, manufacturers can reduce the frequency of replacements, thereby reducing the overall demand for new cables. This, in turn, lowers the carbon emissions associated with repeated manufacturing cycles.
Fiber optic cable:https://www.jera-fiber.com/fiber-optic-cable/
● Improving energy efficiency: Continuous innovation in cable materials and designs can further improve the energy efficiency of data transmission, which will reduce the total carbon footprint throughout the entire life cycle of the cable.
7.Green Certifications and Employee Engagement
Engaging the workforce and achieving green certifications can create a more sustainable work environment and inspire continued progress toward reducing emissions.
● Pursuing environmental certifications: Adopting international standards such as ISO 14001 (environmental management) or LEED certification for energy-efficient buildings demonstrates a commitment to sustainability. These frameworks encourage companies to adopt best practices for reducing waste, managing resources, and lowering emissions.
● Employee awareness and engagement: Educating employees about sustainability practices can drive small, incremental changes in the factory’s overall efficiency. Employees who are aware of the impact of their actions are more likely to support and participate in energy-saving initiatives, further reducing the factory’s carbon footprint.
Conclusion
Reducing the carbon footprint of fiber optic cable factories isn’t just about adopting green technologies; it’s about creating a more sustainable and efficient operation from top to bottom. By improving energy efficiency, embracing renewable energy, optimizing materials, and engaging with circular economy practices, these factories can significantly lower their environmental impact while still meeting the growing global demand for fiber optic technology.
The push toward sustainability is not only beneficial for the environment but also presents opportunities for cost savings, operational efficiency, and improved brand reputation. As industries and consumers increasingly prioritize eco-friendly practices, Jera Line factory that lead the way in reducing carbon emissions will be well-positioned for long-term success.
Post time: Oct-28-2024